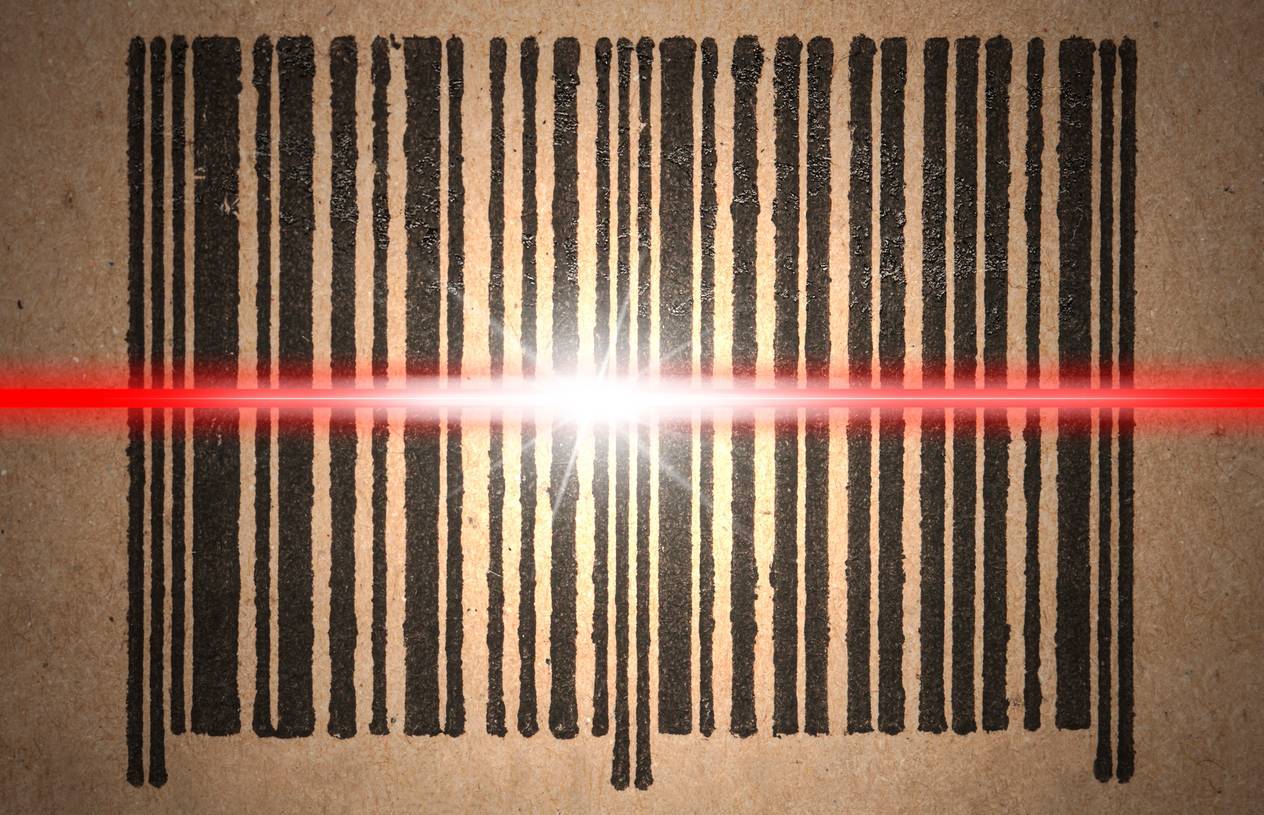
The invention of the barcode for marking and coding was ahead of its time in 1952 when it was granted a patent.
Norman Joseph Woodland and Bernard Silver paved the way for the future of linking an image code to a price or other data.
One problem prevented the idea from taking off until 20 years later – a scanner to translate the barcode.
Now market research projects the business of marking and coding products with various types of barcode designs to reach about $7 billion by 2024. Research and Markets sees the segment growing about 7% each year.
What’s driving the growth of marking and coding?
Few products these days don’t have barcodes. From automotive components, consumer products, and pharmaceutical to that Amazon purchase that UPS or FedEx delivered, the barcode makes quick work of accessing information.
See Inks for Barcoding and Marking
Get Started
Fueling the barcoding demand
- Food and beverage – so-called FMCG (Fast Moving Consumer Goods)
- Stringent global regulations on food and pharmaceuticals
- Liability and product safety concerns
- Increasing automation
- Global supply chain
Why quality barcode-printing matters
The marking icon looks simple enough – a series of lines or other shapes often printed in black.
Any shopper in the self-checkout line knows the frustration of a universal product code (UPC) that won’t scan.
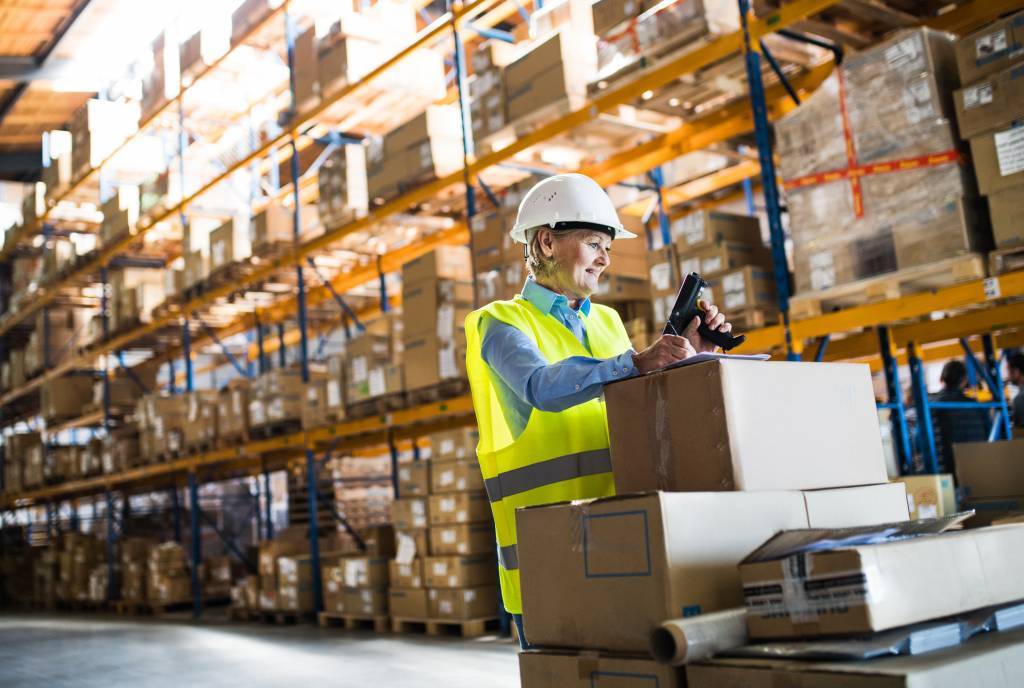
Tracking products and materials in the global supply chain require accurately printed barcodes.
Now, consider the global supply chain, UPS, FedEx, or Amazon. Codes that fail to scan result in lost time, production, and money.
Explore the barcoding inks available for PIJ, TIJ, CIJ printing systems
It may mean the delivery of your package may end up delayed. When placing that 11th-hour-holiday gift, remember that the barcode helps get you that package on time.
Barcodes must be printed consistently.
Achieving a high-quality barcode depends on a combination of factors: printing resolution, ink and contrast, the substrate, the printing environment, and the barcode design. One or more may contribute to a barcode that won’t scan.
How is barcode-quality maintained
Peter Drucker, the sage management thinker and consultant, said, “You can’t manage what you can’t measure.”
The American National Standards Institute (ANSI) established barcode standards in partnership with the Uniform Code Council in 1990. At first, these standards differed from standards in Europe.
Now there are unified standards for two types of symbols.
To further achieve barcode quality, other organizations created their unique standards. The pharmaceutical industry, military, and air-transport companies all have quality standards.
The ANSI/ISO standards for barcodes
Quality for the broadly used one-dimensional (1D) linear barcode relies on measuring and grading nine factors.
The barcodes are scanned with light, often a red laser.
The scanner reads the relationship and other elements of the black and white areas.
-
- Edge determination – The count of the bar-and-space transitions at a fixed point called the global threshold to determine if the barcode is a known type. Grade: Pass/Fail
- Minimum reflectance – Measurement of the darkness (Rmin) of the bar compared to the light reflected by the light bar (Rmax). The dark bar value (Rmin) must be less than half the light reflected (Rmax) by the light spaces.
- Minimum edge contrast – Measures the contrast difference between adjacent bars and spaces. Grade: Pass/Fail
- Symbol contrast (SC) – Determined by subtracting Rmin from Rmax, the higher the contrast, the better the grade. Grade: A-F. An A grade has a score of 70-plus. An F grade has a score of 20 or less.
- Modulation – Measurement of differences in contrast in the barcode. Subtle variations, in contrast readings, create modulation. No modulation would mean that there are no contrast changes in either the dark or light bars. That’s unlikely. Modulation should be kept to a minimum. Modulation uses Edge Contrast and Symbol Contrast in this calculation: Modulation=ECmin/SC. Grade: A-F. An A grade has a score of 70-plus. An F grade has a score of less than 40.
- Defects – Light spots in dark areas or dark spots in light areas, maybe caused by faulty printing equipment or a dirty environment. Grade: A-F. An A grade has a score of 15% defects or less. An F grade has defects of greater than 30%.
- Decodability – It is the margin of error for scanning success from the ideal barcode and the reproduced barcode. It somewhat tricky parameter to understand and control. The more margin of error increases the likelihood of scan success. Decodability may be affected by other quality factors. Grade: A-F.
- Decode – The measurement and pattern of all bars and spaces used in a calculated formula to determine the number content. This measure relates to the accuracy of the dark bars and light spaces. Grade: Pass/Fail
- Quiet Zone – The necessary space on the left and right sides of the barcode must be adequate.
Troubleshooting barcode quality
Troubleshooting poorly printed barcodes involves all components of the printing process being in sync. The substrate impacts the scan success of a barcode in combination with the ink. There must be not only sufficient contrast between the “dark” bars and the “light” spaces, but the reflectivity of the substrate may cause scan failure.
While aluminum cans, for example, may appear to have the necessary contrast, the light reflection or dispersion from the metallic surface may compromise the scan.
The ink, in combination with the substrate, may cause failing grades. An ink that doesn’t dry quickly may absorb and spread, causing modulation errors. Ink matched to the substrate cures quickly with little print gain. When printing on non-porous or glossy substrates, Kao Collins’s new Sigma solvent ink for HP Specialty Printing Systems (SPS) cures fast, reducing print gain. This revolutionary ink also delivers a richer black, producing high contrast. It adheres to many more substrates.
Barcode defects in the light or dark areas may cause scan errors. Here ink defects appear in the light area.
It is critical that the ink solution matches the substrate.
Explore SIGMA solvent ink for HP with 4x decap over other inks
Printing resolution is another factor that may cause a scan failure of the barcode. Printer dpi determines the resolution of the barcode. Higher-resolution printers produce sharper images with well-defined edges.
Defects in light or dark areas may cause scan errors. Here ink defects appear in the light area.
The printhead itself may be the source of defect scan errors. A printhead out of alignment may cause phase errors, incorrect breakups, or poor drop jetting. A printing environment with debris may also cause defect errors.
This barcode has numerous flaws. The black bars have inconsistent inking that could fail for modulation and contrast. The line edges are irregular and there are defects in both the light and dark areas.
Paper particulates or poor substrates may also cause similar errors. Check the printhead and environment to ensure it is clean and properly aligned.
A barcode can be designed and engineered to build a higher margin of error. The inks, substrates, speed, and other factors all contribute to developing a barcode to increase success.
Printing consistent bar codes requires adherence to strict controls. All the components must be matched to achieve optimum results.
Kao Collins’s team of chemists work with customers to determine the ink formulation appropriate for the printer technology and substrate. Testing inks on the intended substrate is the surest method of producing consistent results.
Types of barcodes
What is a 1D Barcode?
Linear symbols use a series of variable-width lines and spaces for data encoding. The Universal Product Code (UPC) barcode is the most common and appears on consumer goods.
Code 39 Code 128 Interleaved 2 id 5 UPC EAN What is a 2D Barcode?
Complex symbols of squares, dots, and other shapes for encoding data. The advantage of 2D codes is that the matrix encodes more information. Supply-chain management generally uses these symbols.
PDF417 Data Matrix QR Contact Kao Collins to talk about getting Sigma Ink for HP. Read more about the new Sigma ink.
READ MORE ON INK TANK
PACKAGING | Inkjet offers flexibility for blister packaging medical products